AzViper
Bronze Member
- Joined
- Sep 30, 2012
- Messages
- 2,038
- Reaction score
- 2,251
- Golden Thread
- 0
- Detector(s) used
- Fisher Gold Bug Pro, Nokta FORS Gold, Garrett ATX, Sun Ray Gold Pro Headphones, Royal Pick, Etc.
- Primary Interest:
- Prospecting
- #41
Thread Owner
Images of the process of cutting, fitting, and welding the base frame. The three holes are the mounting hole of the Unistruct. I am using 3/8" bolts and locknuts. On the underside I enlarged the holes so that I could get a socket to tighten the locknuts. I did not want to use bolt completely through the tubing due to crushing the tubing. Its better to pull the Unistrut tight to the frame using the method shown.
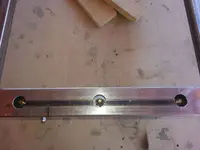
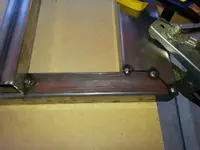
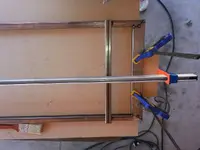
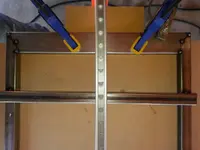
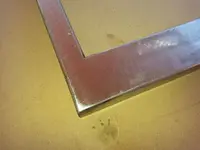
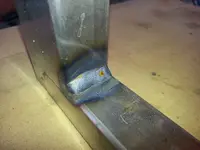
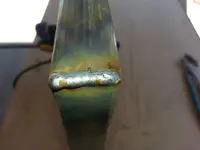
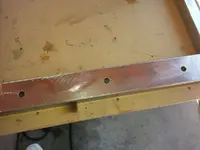
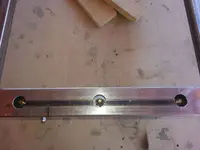
Last edited: