spudnick
Jr. Member
- #21
Thread Owner
We had a saying in the concrete business...."a broom finish can cover a lot of sin". Haha, made me laugh.. You must be old school like me Jim.
Pulse valve update,. I am still waiting on gasket material delivery. But i managed to get a start on the new valve seat. I made a few flat seals from different recycled rubber parts, and settled on the one on top of the valve body. It is 1/2 inch thick solid rubber ( shore A65? ), made from a anti vibration mount ( top left ). I machined a bottom step on it for mounting. The aluminum ring, also has a matching inverse step , that will be the seal lock ring.. I have yet to drill and tap for lock ring fastening.. Also on my list, drill a few more water supply ports in the defuser plate , as the new seal assembly will restrict water flow.. ... FYI,:The recycled suction cup rubber (on right) is interesting. It is 1/4 inch thick rubber , with a metal plate center ( 3/32" ). Keep that in mind for specialty repair and build projects. You can never have too many spare parts kickin around.. Lol.. Ken
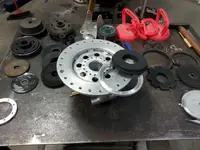
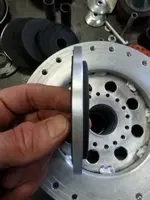
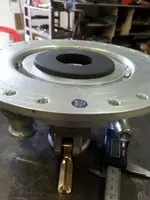
Pulse valve update,. I am still waiting on gasket material delivery. But i managed to get a start on the new valve seat. I made a few flat seals from different recycled rubber parts, and settled on the one on top of the valve body. It is 1/2 inch thick solid rubber ( shore A65? ), made from a anti vibration mount ( top left ). I machined a bottom step on it for mounting. The aluminum ring, also has a matching inverse step , that will be the seal lock ring.. I have yet to drill and tap for lock ring fastening.. Also on my list, drill a few more water supply ports in the defuser plate , as the new seal assembly will restrict water flow.. ... FYI,:The recycled suction cup rubber (on right) is interesting. It is 1/4 inch thick rubber , with a metal plate center ( 3/32" ). Keep that in mind for specialty repair and build projects. You can never have too many spare parts kickin around.. Lol.. Ken
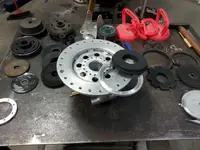
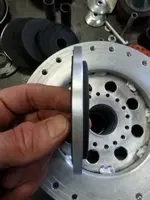
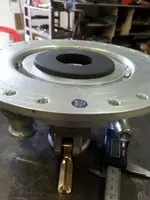