spudnick
Jr. Member
Howdy all, i am in need of valve operation ideas for a water powered pulse valve . I have a mostly built mini portable jig , but i am unable to get the pulse going. It will only vibrate at best.. I have a video of it, will try and load it....Heres a few pictures for now..
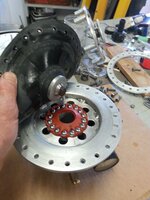
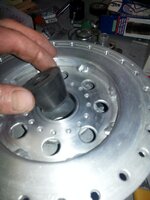
The red 3/16 silicone seal with a aluminum disk was my first valve seat seal attempt. Then i changed to a rubber cone shape seal with a tight fit to the discharge pipe. Both attempts were similar. The water pressure lifts the valve enough to leak and thats it. Just sits there and leaks. Haha. lol. Any advice would be greatly appreciated.... Thanks alot .. Ken P.S.... Thanks to >Jim in Idaho < for his help and knowledge on mineral jigs.. 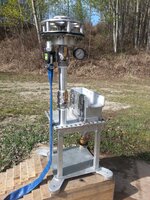
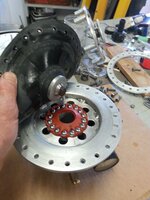
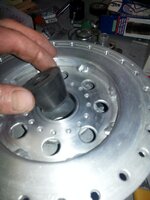
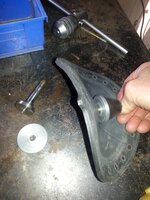
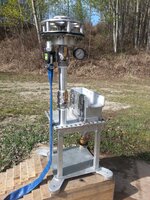