DizzyDigger
Gold Member
- Dec 9, 2012
- 6,391
- 12,973
- Detector(s) used
- Nokta FoRs Gold, a Gold Cube, 2 Keene Sluices and Lord only knows how many pans....not to mention a load of other gear my wife still doesn't know about!
- Primary Interest:
- Prospecting
Made a diligent search for a suitable piece of slate or other appropriate stone material
(ie: affordable), but have decided instead to build using a solid wood top and numerous
coats of chalkboard paint.
Poking around my shop I came up with this old table leaf I'd shoved in the back of
my wood stack some years ago. We gave the table away to a young couple, but they
didn't take the extra leaf as there wasn't room in their dining area for the table to be
any larger than it was.
I checked it using a 5' level, and the surface is perfectly flat from end to end and
side to side.
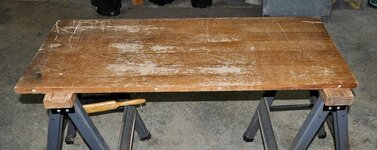
Looks to be solid maple, with a thin layer of hardwood laminate covering the
top. I've since cut it to 16" wide, as there's an area notched along one edge that needed
to be removed, and a 16" width will work just fine. Next step is to sand all that old
stain off, and prepare it for a coat of sealer. (which I'm about done with as I write).
Finished table will be 15-7/8" wide by 43" long.
For a sealer coat I have a full can of Helmsman Spar Urethane, and plan to apply
several coats (to all sides/edges), with sanding between coats to insure a smooth surface.
Pics as it comes along, and as always, I'm completely open to helpful suggestions.
(Just don't get too far ahead of me..
)
(ie: affordable), but have decided instead to build using a solid wood top and numerous
coats of chalkboard paint.
Poking around my shop I came up with this old table leaf I'd shoved in the back of
my wood stack some years ago. We gave the table away to a young couple, but they
didn't take the extra leaf as there wasn't room in their dining area for the table to be
any larger than it was.
I checked it using a 5' level, and the surface is perfectly flat from end to end and
side to side.
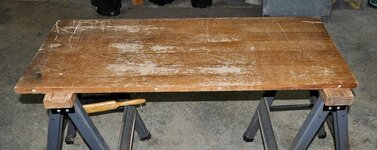
Looks to be solid maple, with a thin layer of hardwood laminate covering the
top. I've since cut it to 16" wide, as there's an area notched along one edge that needed
to be removed, and a 16" width will work just fine. Next step is to sand all that old
stain off, and prepare it for a coat of sealer. (which I'm about done with as I write).
Finished table will be 15-7/8" wide by 43" long.
For a sealer coat I have a full can of Helmsman Spar Urethane, and plan to apply
several coats (to all sides/edges), with sanding between coats to insure a smooth surface.
Pics as it comes along, and as always, I'm completely open to helpful suggestions.
(Just don't get too far ahead of me..

Last edited:
Upvote
0