QNCrazy
Hero Member
Decided last week to finally build a legit power head for my sluice. Made out of 22ga sheet metal. Tack welded and sealed with silicone. First water test failed, lots of leaks. A trip to the hardware store and more silicone did the trick. Here are some pics and video.

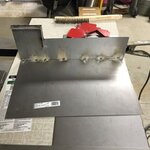
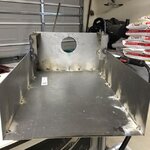
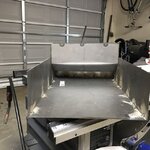
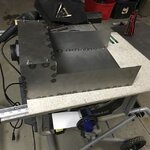
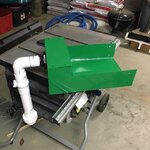
https://youtu.be/Qe0gUlnSdsE
Thanks for looking.

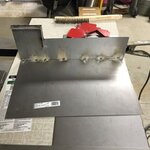
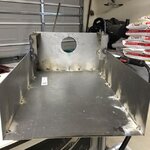
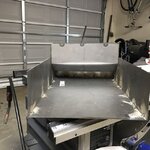
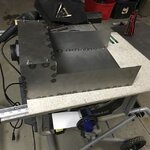
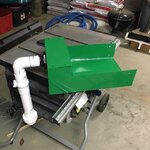
https://youtu.be/Qe0gUlnSdsE
Thanks for looking.